Error Detection with CAD to BIM
Identify and resolve design issues early, before they become costly construction problems.
2D CAD drawings can conceal many design errors that aren't visible until construction begins. Converting your legacy CAD drawings to intelligent BIM models allows us to identify and resolve these issues early—saving time, money, and frustration.
Our CAD to BIM error detection process systematically uncovers inconsistencies, omissions, and conflicts that would otherwise lead to expensive rework, delays, and disputes on the construction site.
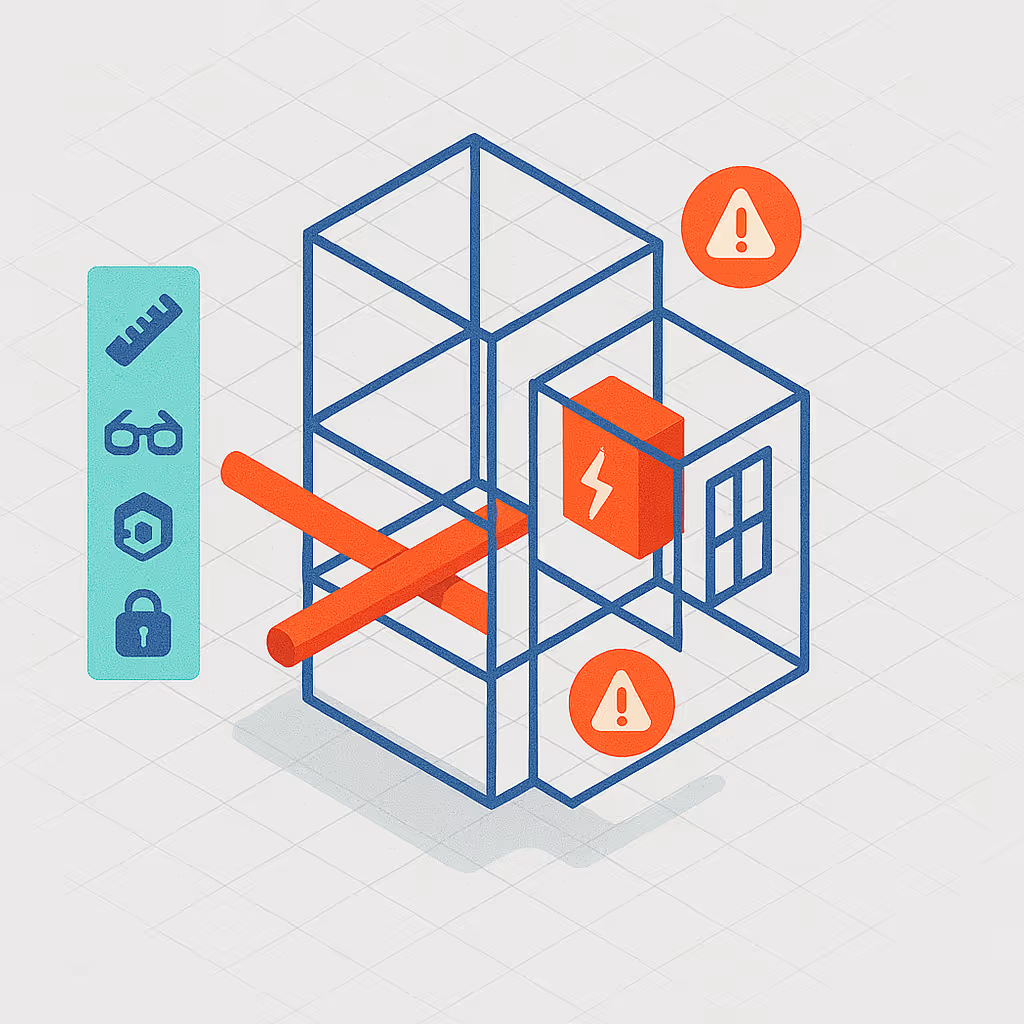
Types of Errors We Detect
Our CAD to BIM conversion process identifies multiple categories of design issues:
- Geometric Inconsistencies - Mismatched dimensions, improper alignments, and inaccurate scaling issues that can cause construction problems.
- Spatial Conflicts - Elements occupying the same space, improper clearances, and access issues that impact functionality and code compliance.
- System Interferences - Clashes between structural, architectural, and MEP systems that would cause rework during construction.
- Documentation Gaps - Missing information, incomplete detailing, and ambiguous specifications that lead to RFIs and delays.
- Code Violations - Non-compliance with building codes, accessibility requirements, and industry standards that could cause permit issues.
Our Error Detection Process
Initial CAD Analysis
We carefully review your CAD drawings to identify obvious inconsistencies, missing information, and potential problem areas.
3D Model Development
We create intelligent Revit models from your CAD files, revealing spatial relationships that aren't visible in 2D.
Automated Checking
We apply rule-based validation tools to identify geometry issues, duplications, intersections, and other conflicts.
Manual Verification
Our BIM specialists review the model through multiple perspectives and sectional views to identify issues missed by automated tools.
Documentation & Resolution
We provide detailed reports of all identified issues along with recommendations for resolution and corrected model elements.
Impact on Project Success
Detecting errors during the CAD to BIM conversion process delivers significant benefits:
Cost Savings
Resolving an issue in design typically costs 1/10th of what it would cost to fix during construction. For major conflicts, this can mean savings of tens of thousands of euros per issue.
Schedule Protection
Early issue detection prevents the construction delays that occur when problems are discovered on-site. Each avoided on-site issue can save days or weeks in the schedule.
Reduced Disputes
Clearer documentation and resolved conflicts mean fewer disagreements between contractors, subcontractors, and owners about responsibility and change orders.
Higher Quality
A thoroughly vetted design leads to better construction quality, fewer defects, and improved long-term building performance.
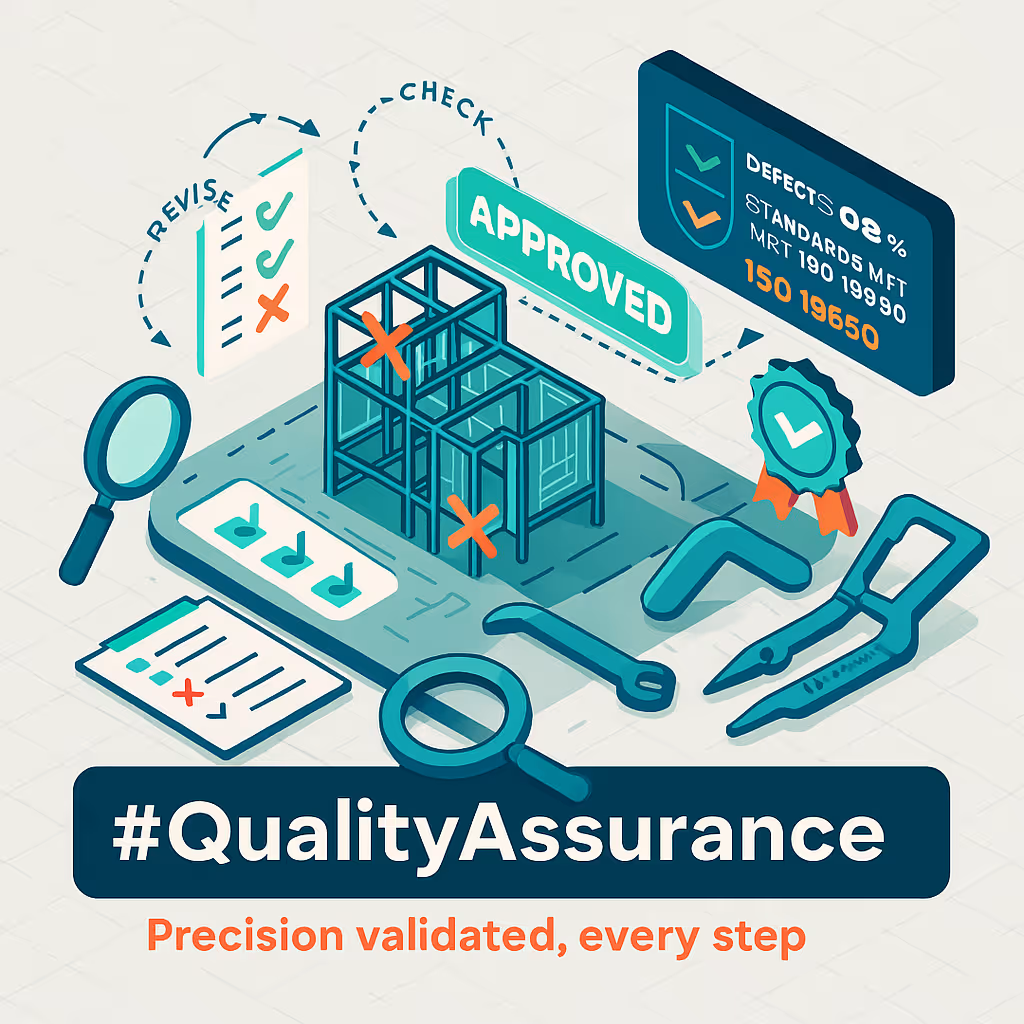
Error Detection in Action

Office Building Renovation
A 5,000 m² office building renovation relied on 15-year-old CAD documentation that had been updated inconsistently over time. During our CAD to BIM conversion process, we identified:
- 62 significant structural/MEP conflicts that would have caused major rework
- Outdated building systems that didn't meet current energy codes
- Several areas with inadequate ceiling space for planned new ductwork
- Missing accessibility provisions required by updated regulations
By identifying these issues early, the client was able to update their design before tendering, avoiding an estimated €180,000 in change orders and keeping their 10-month construction schedule intact.
Related Services
Ready to Identify and Resolve Design Issues?
Contact us to discuss how our CAD to BIM error detection can improve your project outcomes and prevent costly mistakes.